For decades, quality control in manufacturing has relied heavily on human visual inspection or mechanical testing methods. Traditional inspection techniques include manual checks by workers and using gauges, microscopes, and other measuring tools to detect visible and structural product defects. While foundational, these methods are often time-consuming, subject to human error, and inconsistent due to variability in human judgment and physical fatigue.
AI Inspection and Its Relevance to Modern Manufacturing
As industries strive for greater efficiency, accuracy, and reduced costs, Artificial Intelligence (AI) is increasingly becoming a game-changer. In manufacturing, AI technologies can process and analyze vast amounts of data beyond human capability, leading to more precise operations, predictive maintenance, and enhanced defect detection.
AI visual inspection, through pattern recognition, significantly improves the ability to detect defects in manufacturing processes, employing deep neural networks, such as deep convolutional neural networks (DCNNs), for tasks like weld flaw detection, object detection, crack detection, and non-destructive testing (NDT). This integration of computer vision methods using DCNNs shows exceptional promise for applications requiring high accuracy in defect detection.
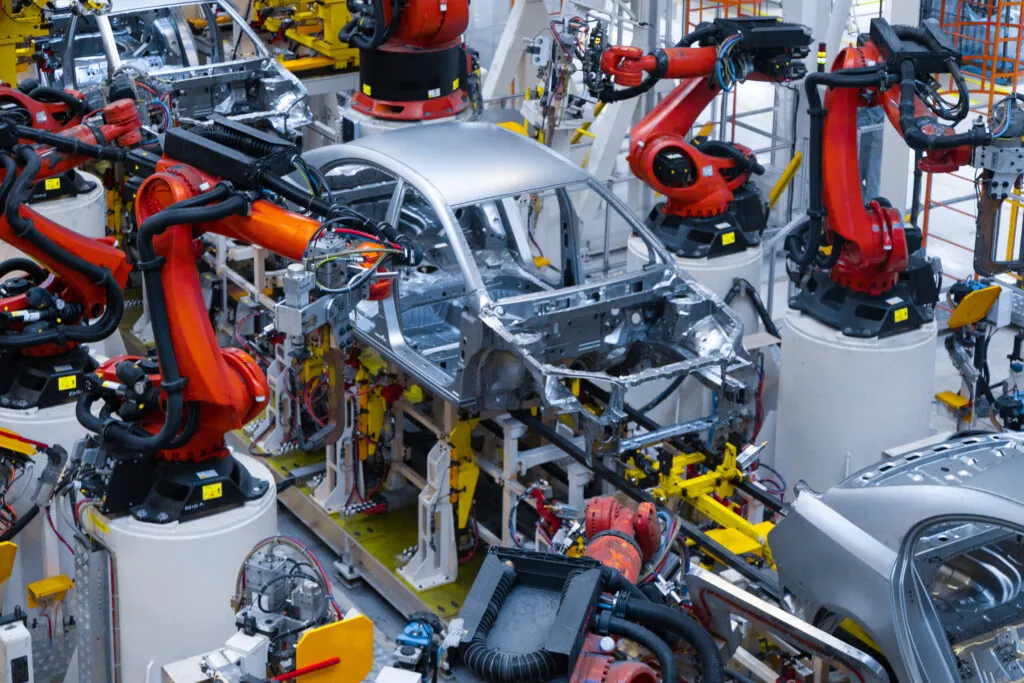
The Shift to AI-Driven Visual Inspection in Manufacturing
Manual inspection methods, while traditional, present several inherent limitations that can undermine the efficacy of quality control in manufacturing. The accuracy of these methods often depends on the skills and experience of human inspectors, which can vary significantly. This variability introduces inconsistency in detecting defects, especially in complex or high-volume production scenarios.
Moreover, manual inspections are labor-intensive and time-consuming, leading to higher operational costs and potential bottlenecks in production lines. Fatigue and human error further compound these issues, sometimes resulting in overlooked defects that could compromise product quality and safety.
Overview of the Evolution from Manual to Automated Systems
The evolution from manual to automated systems in manufacturing has been driven by the need to overcome the limitations of human inspectors. Initially, this transition involved using simple computerized tools that could perform repetitive tasks more consistently than humans. However, automation has become increasingly sophisticated with technological advancements, especially machine learning and computer vision development.
These systems can now detect a wide range of defects, including surface defects, with greater precision and faster rates than traditional methods. Automated systems, particularly those utilizing AI, are adept at detecting surface defects in products by leveraging advanced techniques such as convolutional neural networks (CNN) and unsupervised learning, addressing challenges like complex textures, noise, and variations in lighting conditions.
Integrating sensors, cameras, and software has enabled continuous monitoring and analysis of products on the assembly line, marking a significant leap in manufacturing technology.
Advantages of AI in Enhancing Accuracy and Efficiency
AI-driven visual inspection systems benefit manufacturing processes, enhancing accuracy and efficiency. By utilizing advanced algorithms, these systems can analyze images and identify defects with precision far exceeding human capabilities. This accuracy is crucial for ensuring products meet strict quality and regulatory requirements.
Additionally, integrating AI in these systems plays a pivotal role in minimizing the number of detected defects, thereby significantly enhancing product quality and manufacturing efficiency. AI systems can operate continuously without fatigue, processing large volumes of products at speeds unattainable by human inspectors. This increase in throughput boosts production efficiency and reduces the time to market for products.
Furthermore, AI-driven systems can adapt and improve over time through machine learning, continually enhancing their ability to detect new or evolving types of defects.
Deep Learning: The Driving Force Behind Automated Defect Detection
Deep learning, a subset of machine learning, has emerged as a pivotal technology that enables more sophisticated and reliable automated defect detection systems in manufacturing. This section delves into how they enhance AI systems’ capabilities and compares various deep learning models utilized in defect detection.
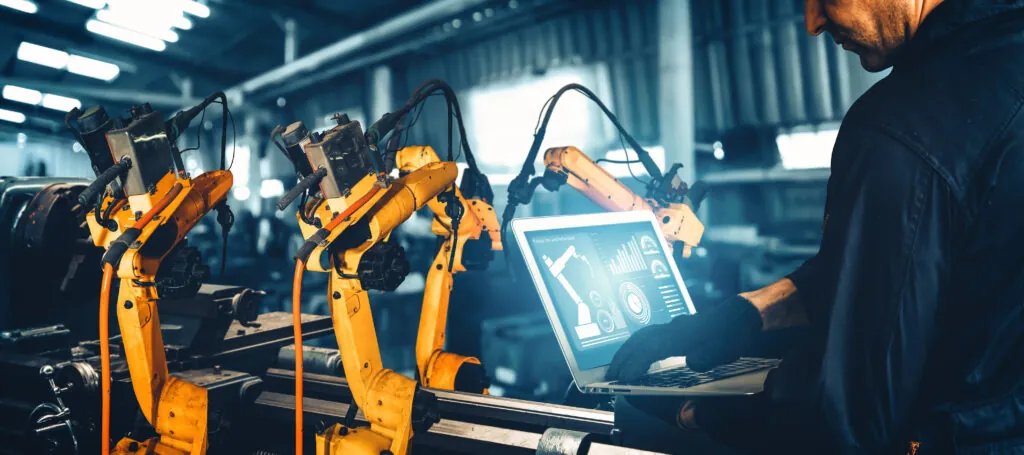
How Deep Learning Improves the Capabilities of AI Systems in Recognizing Complex Defects
Deep learning models, especially Convolutional Neural Networks (CNNs), are adept at handling image data. In defect detection, CNNs can identify intricate patterns and anomalies in product images invisible to the human eye. For example, a CNN can distinguish between a minor variance in color or a slight misalignment that may indicate a defect, learning from thousands of examples of what constitutes a defect.
Deep Learning Models Used for Defect Detection
Several deep learning models are employed for defect detection, each with unique characteristics suited to different types of defects and manufacturing processes:
- Convolutional Neural Networks (CNNs): Ideal for image-based defect detection, CNNs excel in processing pixel data and maintaining spatial hierarchy between pixels, making them perfect for detecting shape and texture-based anomalies.
- Autoencoders: These models are adequate for unsupervised learning scenarios where labeled data is scarce. Autoencoders can learn a compressed representation of normal objects and then detect anomalies by measuring the reconstruction loss. This approach is beneficial for detecting unexpected types of defects.
- Recurrent Neural Networks (RNNs) and Long Short-Term Memory Networks (LSTMs): These models benefit production processes where temporal data is crucial, such as detecting defects in continuously produced materials like textiles or wires. They can analyze sequences of images or sensor readings to identify abnormalities over time.
- Generative Adversarial Networks (GANs): Used for more advanced applications, GANs can generate synthetic data that augments the training dataset, especially useful in scenarios where certain types of defects are rare.
Deep learning models have significantly advanced the field of automated defect detection by improving detection accuracy, reducing false positives, and enhancing the ability to adapt to new or changing types of defects without extensive reprogramming. This capability has made deep learning an indispensable tool in the modern manufacturing industry, ensuring products meet quality standards efficiently and consistently.
Computer Vision as an Optical Defect Detection Technology
Computer vision has become a cornerstone technology in automated defect detection within manufacturing. It leverages the power of visual processing to analyze and interpret images from the production line to detect abnormalities or defects. Here, we will introduce computer vision, explore its critical components, and provide a case study to illustrate its application in defect detection.
Download FREE ebook – AI-Enhanced Computer Vision in Manufacturing
What is Computer Vision?
Computer vision is a field of artificial intelligence that trains computers to interpret and understand the visual world. Using digital images from cameras and videos and deep learning models, computer vision systems can accurately identify, classify, and react to elements within images.
The critical components of a computer vision system in manufacturing include:
- Image Capture Devices: High-resolution cameras and imaging equipment designed to capture detailed images or videos of products on assembly lines.
- Preprocessing Tools: Software algorithms enhance image quality and format the data by correcting distortion, enhancing contrast, or removing noise.
- Feature Extraction Techniques: These algorithms detect and isolate various attributes or characteristics within an image, such as edges, textures, or specific shapes.
- Classification and Machine Learning Models: At the core of defect detection, these models analyze extracted features to determine whether a product meets quality standards or contains defects.
- Feedback Systems: Components that allow the system to act based on the vision system’s output, such as rejecting a defective product or alerting a human operator.
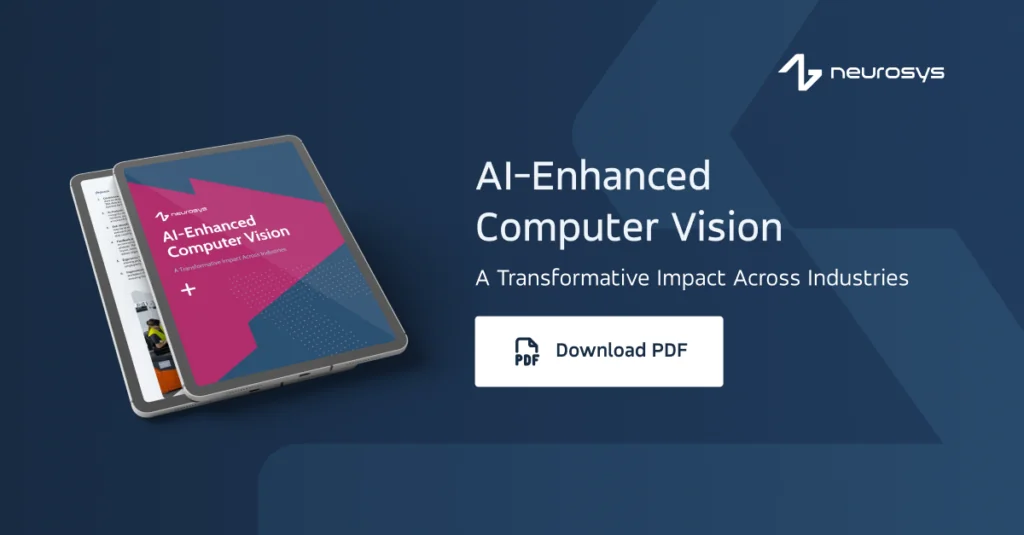
Detailed Examination of How Computer Vision Interprets Manufacturing Images
In manufacturing, computer vision systems are primarily used for quality assurance by inspecting images for defects. Here’s how the process typically unfolds:
- Image Acquisition: The system captures real-time images of each product as it passes through the production line.
- Preprocessing: Images are preprocessed to ensure consistency and enhance features necessary for the subsequent analysis.
- Feature Extraction: The system uses various techniques to extract distinctive features from the preprocessed images. This might include identifying specific patterns, textures, or dimensions.
- Defect Detection: Using trained machine learning models, the system compares extracted features against predefined patterns of non-defective items. Deviations from these patterns are flagged as potential defects.
- Action: The system automatically sorts out defective products or sends alerts for further inspection.
Implementing AI Defect Detection System in Manufacturing
AI detects defects in manufacturing processes primarily by integrating machine learning and computer vision technologies. Here’s a detailed breakdown of how AI accomplishes this task:
Data Collection
AI systems begin with data collection, which is critical for training and operational purposes. In manufacturing, data collection typically involves capturing images or videos using cameras and sensors installed along the production lines. This data might include pictures of items as they are being produced, which helps the AI system learn what a “good” product looks like and identify deviations that indicate defects.
Data Preparation and Annotation
Once data is collected, it needs to be prepared and annotated. This process involves labeling the images or video frames to indicate whether a product is defective and, if so, highlighting the specific areas of defect. Data annotation is crucial because it trains the AI model to recognize and differentiate between defective and non-defective products.
Model Training
With annotated data, the next step is training the AI model, typically a deep learning model such as a convolutional neural network (CNN). During training, the model learns to associate specific patterns in the image data with the presence of defects. Over time, and through exposure to numerous examples, the model optimizes its internal parameters to minimize errors in predicting defects.
Model Testing and Validation
After training, the AI model is tested and validated using new images not seen during the training phase. This step is crucial to ensure the model performs well on unseen data, simulating real-world operations where every new product on the line could have different defects.
Real-time Inspection and Feedback
Once validated, the AI model is deployed into the manufacturing environment to inspect products in real time. Cameras and sensors capture images that the AI model instantly analyzes as products pass through the production line. If defects are detected, the system can immediately flag and reject the item or alert human operators to intervene, depending on the setup.
Continuous Learning and Adaptation
An advanced feature of AI systems is their ability to learn and adapt continuously. By incorporating feedback mechanisms, the AI system can learn from new defects and errors, adjusting its parameters to improve detection accuracy over time. This adaptability is particularly useful in dynamic manufacturing environments where product designs and materials change frequently.
AI-driven defect detection systems offer higher accuracy, faster processing, and the ability to learn and adapt to new challenges automatically. This approach enhances product quality and significantly improves manufacturing processes’ overall efficiency and productivity.

Conclusion
As the manufacturing landscape evolves, AI visual inspection technologies are revolutionizing how industries approach quality control and defect detection. Employing advanced deep learning and computer vision systems, manufacturers can now detect even the slightest anomalies with unprecedented precision and efficiency.
If you’d like to discuss integrating or enhancing AI capabilities in their production lines, join a free consultation with a NeuroSYS expert.