It’s not about buzzwords or temporary crazes, it’s all about solutions that work. This time we’ll delve deeper into digital transformation in industrial manufacturing, helping the working people worldwide.
Manufacturing, one of the main pillars of the global economy, is heavily dependent on technology use. Even before the common electrification, production plants adopted the most modern solutions to streamline production, achieving the highest possible efficiency.
The Industry 4.0 era led the transformation far beyond manufacturing machinery. The Fourth Industrial Revolution takes place right before our eyes. The times of production plants relying on error-prone manual labor, extensive paperwork, repetitive tasks, and dispersed expert knowledge goes out of date.
Now it’s the time to shine for digital technology in manufacturing.
What are the 4 main areas of digital transformation?
Digitization of manufacturing operations to create new processes, new quality, and new products occurs in the below areas:
Business model transformation
When the current offer does not suffice the market demand anymore, companies switch to a different, digital business model.
Domain transformation
Some market fields become a thing of the past or turn out unprofitable. The obvious solution is moving the business to a different domain, redefining offered products and services.
Process transformation
Remaining competitive in the market requires a change in the execution of those company processes which have become inefficient or obsolete. Whether the amendments are small or comprehensive, modernization allows for achieving new goals.
Organizational transformation
Manufacturing does not solely focus on machines and processes, and there is also a human aspect of transformation that needs to be addressed.
Why digital transformation is important in manufacturing?
Those who don’t adapt stay in place. While small family businesses and local workshops often don’t feel the need of technological improvements, global enterprises set a direction for the industry. Digitalization of manufacturing is brought down to satisfying customer needs, responding to market changes, achieving optimal efficiency, and making profits. The more extensive the operational scope, the greater the range of possibilities.
How is digitization transforming the manufacturing industry?
Digital in the industry – a broad and diverse range of applications. Below you’ll find some of the by far, most remarkable examples of digital transformation in manufacturing.
Internet of Things
Solutions like condition monitoring sensors become more and more popular in the manufacturing sector. The reason behind it is the convenience the devices offer in tracking the health statuses of equipment, machinery, and the facilities as a whole in real-time. Since the staff needs to intervene only if the sensors detect abnormalities (or respond according to preloaded preferences), less human attention is needed to monitor the production plant condition.
Artificial intelligence
More and more manufacturing plants carry out their processes under the watchful eye of AI. The use of computers capable of performing tasks usually associated with humans, spans various fields. Manufacturing processes generate huge amounts of data, analyzing which helps to determine the variables crucial for production operations.
There are many applications of AI in manufacturing companies, such as Generative Adversarial Networks (GAN) used in generative design, predictive maintenance, and analysis, used to forecast occurrences (malfunctions and downtimes) potentially threatening operational continuity, and algorithm-powered quality assurance processes.

Augmented and virtual reality
Supplementing (or substituting) the physical world with digital enhancements is widely used by industrial companies. Technicians equipped with dedicated wearable devices are able to execute tasks ranging from hands-on training, and maintenance operations, to remote factory acceptance testing, at the same time, remaining in touch with experts located anywhere in the world. AR and VR shorten the processes requiring on-site presence when carried out the traditional way.
Assisted reality solutions contribute to strengthening internal knowledge management by aggregating expertise in a standardized, easily accessible way. Using digital tools in the competency-building process allows for delivering more engaging content. It is also possible to reduce the costs of training (less workload of trainers, no classrooms or paper tutorials). Digital learning platforms help retain knowledge, by protecting internal know-how from outflowing when experts leave the organization. Solutions like the Nsflow AR platform, designed with the industry in mind, improve industrial operations, helping address the problems faster and more efficiently.
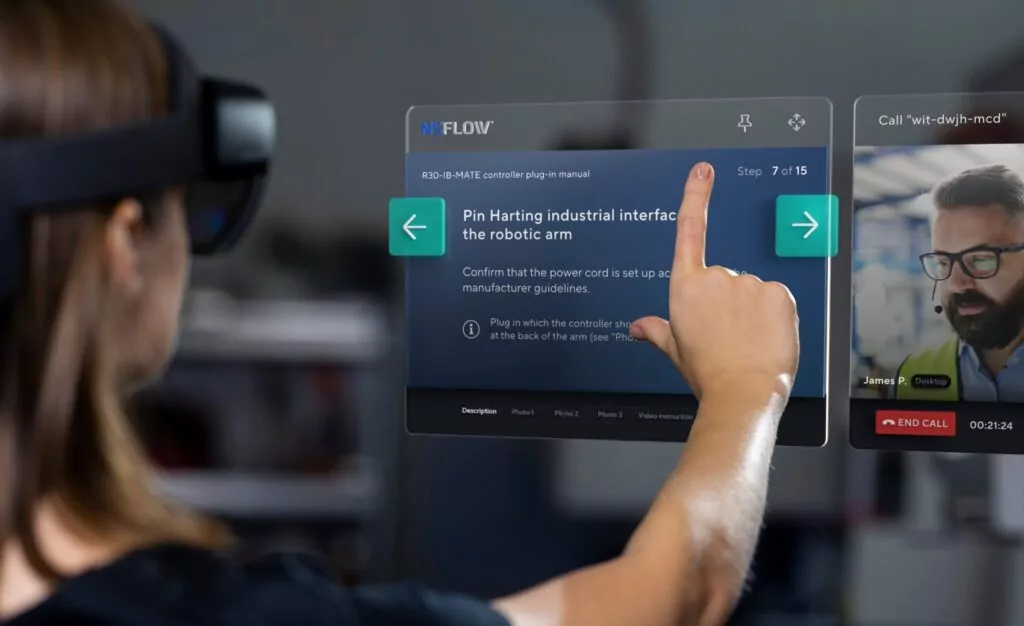
Big Data
Using Big Data technology manufacturers can conveniently track and analyze their process data. Understanding the data behind operations helps to solve issues previously unnoticeable or difficult to detect using traditional methods. Finding patterns and relationships enables providing better solutions and carrying out processes in a modern environment. Big Data is successfully used in executing quality checks, streamlining supply chains, detecting areas for optimization, and improving overall efficiency.
Data analysis is the foundation of another practice crucial for modern production plants: manufacturing analytics. As manufacturing machinery creates streams of data, companies turn to using them for forecasting demand, maintenance optimization, order optimization, and risk management. The process of acquiring, arranging, and analyzing data is vital for preventing breakdowns, identifying areas for enhancement, and predicting future applications – in a more comprehensive manner than an individual would do.
Automation
Ceding tasks to technology reduces the need for human input. The manufacturing industry and its processes are one of the most grateful fields for automation. The term covers several types of automation: flexible (with programmable computerized systems controlling the machines, great for batch production and assembly lines), fixed (the so-called hard automation, combining various sequences in the production of large quantities e.g. material conveyor systems), and programmable (good for machines used for various tasks, e.g. industrial robots, where reprogramming allows the system to execute different sequences).
Digital twins
Using a digital representation of physical objects allows for applying more immersive and life-like examples than traditional CAD models. With the dedicated software, manufacturers can shorten processes, reduce the need for building physical prototypes, which results in executing design and production processes faster. Industries successfully adopted the digital twin concept as a part of the smart manufacturing approach, utilizing extensive datasets to visualize their products.
Why is digital transformation a challenge for manufacturers?
Transforming digitally is no small feat for manufacturers and requires overcoming several obstacles on the way. Some of these challenges include:
Skills
Retaining expert knowledge and preserving internal know-how. Bearing in mind phenomena like the Great Resignation and the ongoing generational change, companies need to protect their expertise and ensure its efficient transfer to the newly incoming employees. Filling in the generational gap will involve training approximately 2 mln new employees globally, many of which represent the younger generations. As such, new hires may require a different approach to learning to remain motivated and efficient.
Costs
Extensive investments may seem like a significant cost, but missed opportunities, knowledge outflow, recurring downtimes, and losing to the market leaders is the cost companies pay when not adapting to the changing environment.
The right solutions
it’s not about using something digital just for the sake of it or because everyone does it. To make it even harder, there’s no such thing as a universal path to follow. Benefitting from digital transformation services requires an in-depth understanding of ongoing processes and ways technology can improve them. (The good news is we’re here to help and assist you in the strive to transform your operations digitally.)
The impact of digital transformation on manufacturing
Does the manufacturing industry need to transform digitally? Taking into account all the above examples, it is clear that revamping the processes and implementing the latest technologies is essential for remaining competitive and delivering value.
Benefits of digital transformation in manufacturing
Digital transformation in the manufacturing industry needs to bring tangible results, as enterprises won’t turn their processes upside down just for the sake of digital advancement. The business has its own rules according to which, the efforts put into the transformation should bring profits. Therefore, it’s worth pointing out some of the advantages arising from the digitalization of manufacturing?
Improved efficiency
Less time spent on repetitive, mundane tasks, better allocation of resources, and improved workforce management.
Enhanced safety
Advanced recognition of hazards, reduced need for workforce performing potentially dangerous tasks, and more precise execution of tasks.
Greater competitiveness
Strengthened market position through introduced innovation, future-proofed processes, and greater value delivered to customers and stakeholders.
Savings
Reduced labor costs, effective avoidance of human error and machinery downtimes, and reduced spending on business travels and training expenses.
Digital technologies enter production processes and power the industry. The changes may not be occurring dynamically, as extensive processes and production plants require some time to adjust to new conditions. The business is certainly adapting to the new reality of Industry 4.0. The accelerating change is rather unlikely to fluctuate anywhere in the foreseeable future. The traditional industry we used to know, is becoming a thing of the past. It’s time for digitally enhanced manufacturing, benefiting from technological advancements and maximizing its potential.
Are you considering a digital transformation for your company? Did any of the top digital transformation trends in manufacturing catch your attention? Seek no more – book your one-hour free consultation and find out how technology can streamline your operations.
Read more:
Digital transformation in healthcare
Digital transformation in banking and financial services
Benefits of digital transformation
How to measure digital transformation