2024 is the last call to delve into the Internet of Things (IoT), which, next to artificial intelligence and VR/AR, remains one of the three main priorities of corporate technologies. There is also a growing tendency to combine IoT and artificial intelligence, which is perceived as a good direction for developing this technology market segment, worth USD 236 billion in Q4 2023 (source).
The idea of the Internet of Things is a digital ecosystem in which physical objects-devices have artificial intelligence that allows them to sense, communicate, and interact with the environment. It extends the capabilities of the Internet beyond traditional computers and smartphones to include a wide range of physical objects equipped with smart sensors, actuators and other technologies.
Most importantly, predictive maintenance with IoT technology yields numerous benefits for industries and businesses. It is intended to increase the efficiency and productivity of machines, which is the purpose of popularizing predictive maintenance (PdM) with IoT systems. Thus, in this article, you will discover multiple ways predictive maintenance with IoT boosts the manufacturing industry.
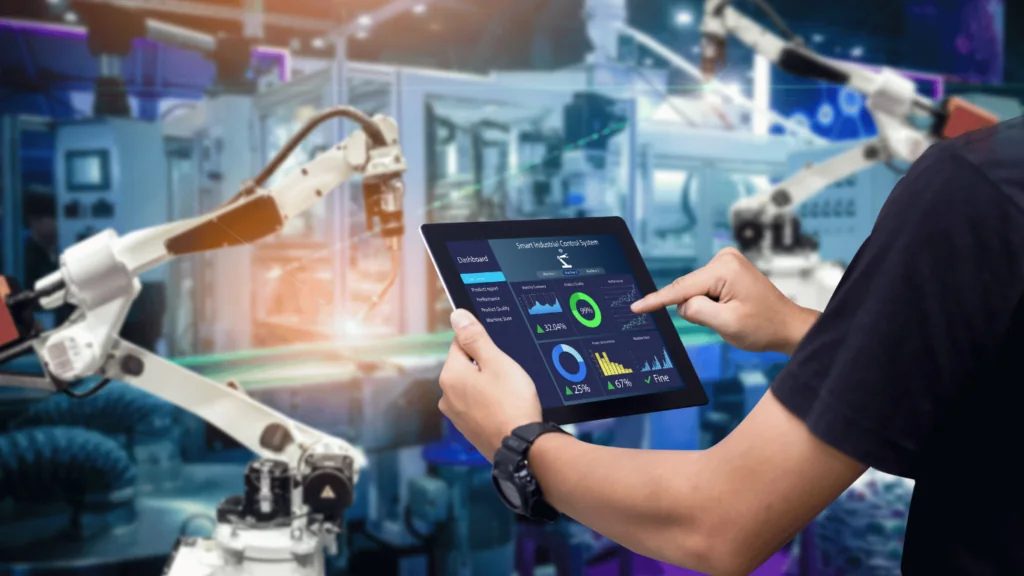
Predictive Maintenance With IoT – How Is It Connected?
The model predictive maintenance system with IoT technology is based on three pillars. The first is hardware, which means various IoT devices that collect data (read more in the next paragraph). The second is software, i.e., AI algorithms for processing and analyzing this data; the third is communication between the hardware and the computer. Below, we explain basic IoT role and place in predictive maintenance:
IoT Sensor Integration for Data-Driven Maintenance
The general IoT equipment includes sensors, actuators, intelligent meters, IoT gateways, and programmable logic controllers (PLCs). It must be distributed appropriately on machines and production lines and connected to the computer. The most important are IoT sensors, which collect data, including parameters such as temperature, vibration, pressure, etc.
IoT sensors make predictive maintenance models much more accurate by giving researchers a large dataset, allowing them to make more accurate predictions about when equipment will break down. For instance, IoT sensors installed on machinery in manufacturing plants detect deviations in vibration patterns, signaling potential issues with bearings or other components. This early detection empowers maintenance teams to address emerging problems promptly, preventing costly downtime and optimizing equipment performance.
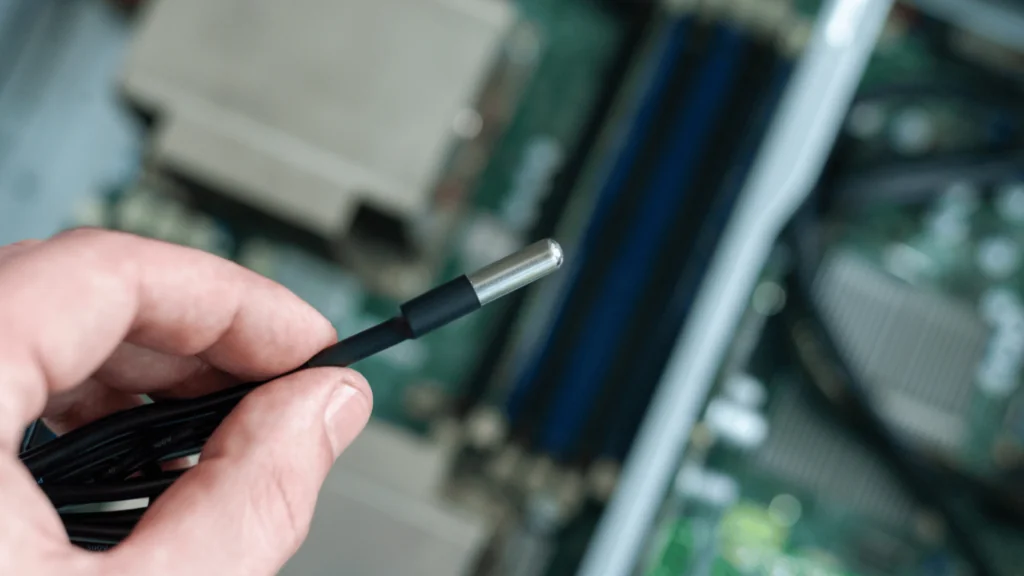
Typical sensors in manufacturing IoT systems include temperature, pressure, humidity, vibration, and proximity sensors.
Data Analysis and Predictive Modeling
Data analysis serves as the cornerstone of predictive maintenance with IoT, involving the processing and analyzing vast amounts of data generated by IoT sensors connected to computer systems. IoT operates on artificial intelligence algorithms in predictive maintenance systems, particularly leveraging machine learning (ML) and advanced data analysis. These algorithms actively compare current and historical data, enabling continuous optimization of machinery and device operations. Artificial intelligence empowers computers to learn from data, enabling them to predict potential failures, optimize maintenance schedules, and enhance machine efficiency. By applying sophisticated data processing techniques, these algorithms actively identify patterns and anomalies in the data, laying the foundation for predictive modeling.
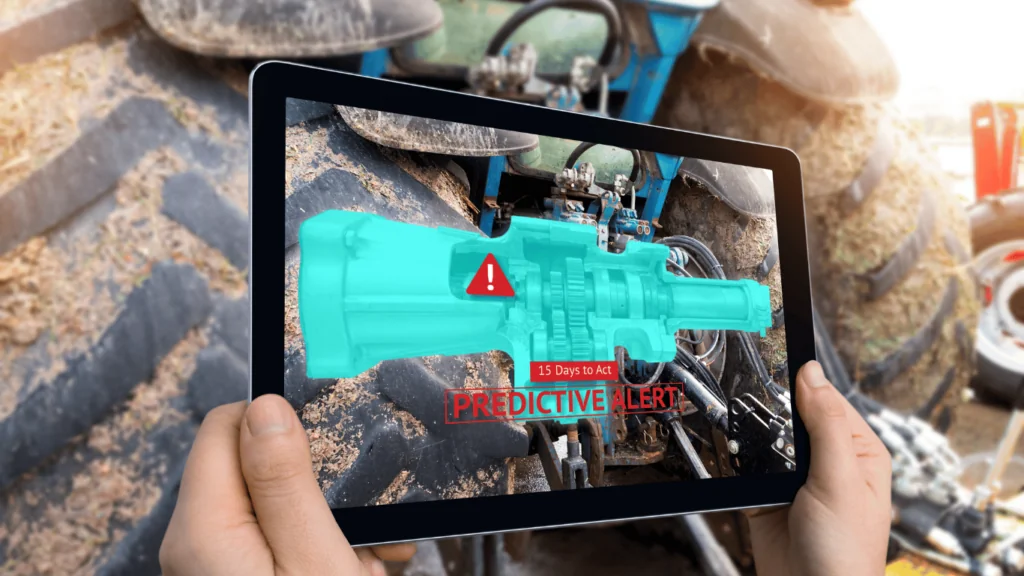
Through the application of advanced data processing techniques, AI algorithms within IoT systems actively discern patterns and anomalies in data, thereby establishing the groundwork for predictive modeling.
Real-Time Monitoring and Warning Systems
One crucial advantage of predictive maintenance with IoT technology lies in its ability to actively monitor equipment health in real-time. Manufacturers benefit from immediate insights into equipment performance and condition as data from IoT sensors is continuously fed into centralized monitoring systems. This real-time monitoring empowers maintenance teams to address emerging issues before they escalate into major failures proactively.
For example, in the manufacturing industry, IoT monitoring systems actively identify abnormal fluctuations in temperature or pressure in pipelines, indicating potential leaks or ruptures. IoT warning systems actively mitigate safety risks and prevent costly environmental damage by promptly alerting operators to these anomalies.
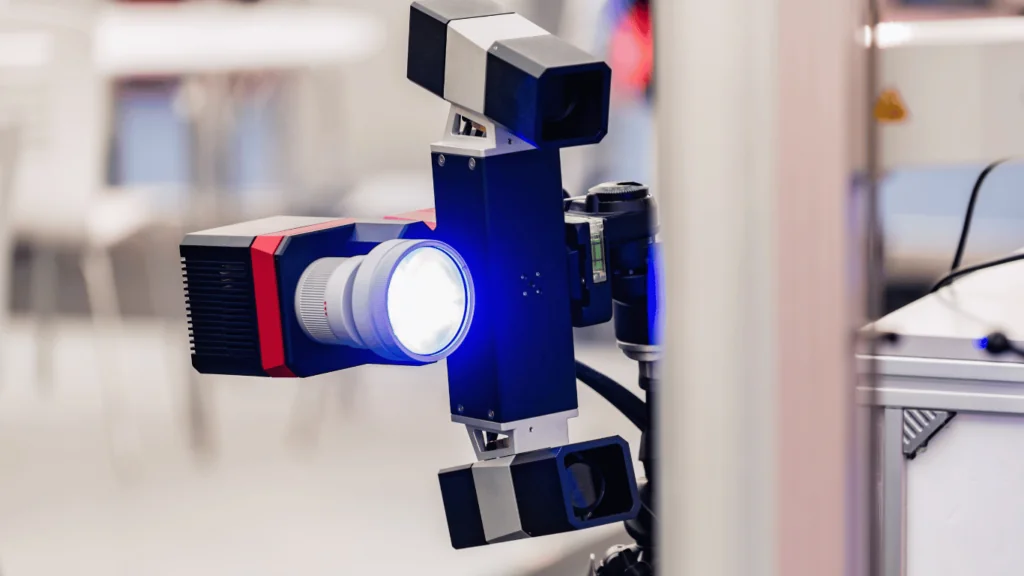
Predictive Maintenance With IoT – Main Benefits In Industry & Business
Predictive maintenance with IoT brings many benefits to industry and business. These benefits concern both the overall improvement in production efficiency, employee safety and savings made from better use of available resources. Below we describe in detail how IoT technology coupled with predictive maintenance will improve operational efficiency in the manufacturing industry:
Increased Operational Efficiency
Predictive maintenance based on IoT systems offers many benefits, especially regarding operational efficiency, production processes and, more generally, business. All thanks to proactive identification of potential equipment failures. By analyzing data collected by IoT sensors, AI algorithms can detect early signs of wear and tear, enabling timely intervention before failure occurs. This reduction in unplanned downtime not only ensures smooth operation of production lines, but also minimizes operational disruptions. The result is maximized operational efficiency.
Cost Reduction
Predictive maintenance with IoT reduces costs in two ways. Firstly, by reducing the need for emergency repairs, and secondly, by avoiding costly production downtime. By forecasting maintenance needs based on data provided by smart devices and comparing this data with historical trends, industrial companies can plan maintenance activities during scheduled downtime (when machines are not working anyway). In this way, PdM helps optimize resource allocation and minimizes the impact of lengthy repairs on production schedules. This approach prevents potential loss of revenue due to unexpected equipment failures.
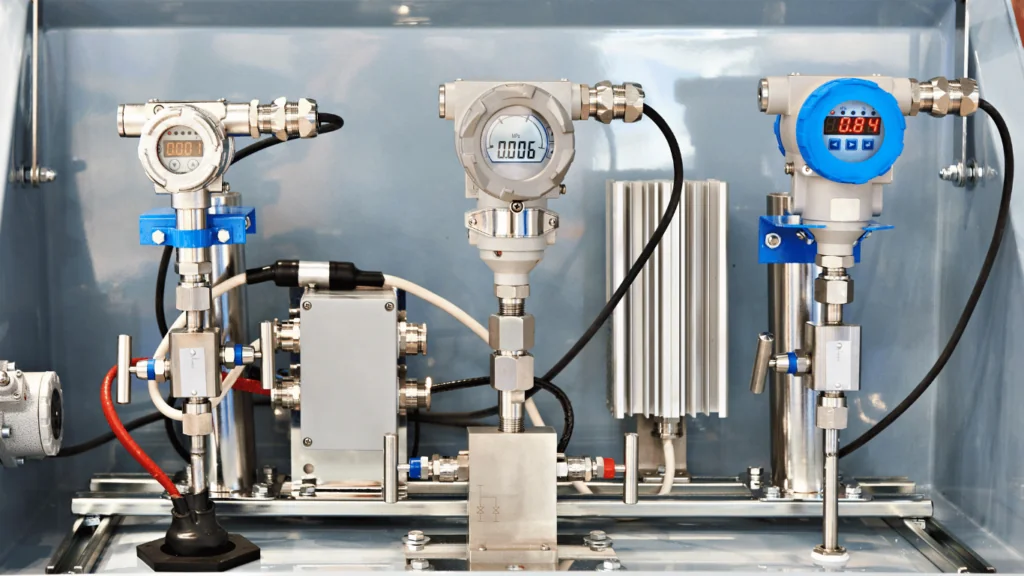
Predictive maintenance with IoT boosts operational efficiency, productivity, and safety while optimizing resource use, leading to significant cost savings.
Machine and Equipment Management
IoT technology plays a key role in asset management. Predictive maintenance with IoT gives insight into the life cycle of these resources and enables their optimal use. This includes a wide variety of devices and systems:
- production machines and equipment,
- production lines with interconnected machinery and equipment,
- transportation and logistics equipment, including vehicle fleets,
- instrumentation and control systems,
- utility systems,
- facilities and infrastructure.
Additionally, by monitoring equipment health and performance, IoT sensors enable companies to identify maintenance needs and prioritize tasks based on their criticality. This ensures the efficient allocation of resources, extending the life of assets and maximizing return on investment.
How Predictive Maintenance With IoT Ensures Safety and Reliability in Industry
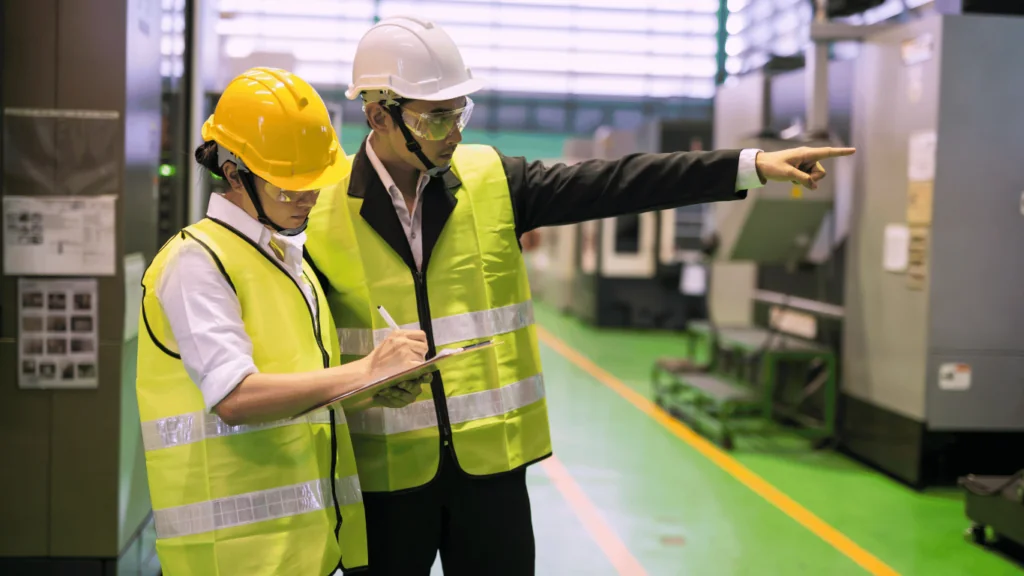
Predictive maintenance, coupled with IoT technology, is a powerful solution to address these concerns comprehensively. By harnessing real-time data and advanced analytics, PdM strategy enhances operational efficiency and plays an important role in ensuring safety and reliability across various industrial sectors. Here are some examples:
Risk Reduction
Let’s also emphasize that predictive maintenance with IoT is a proactive risk mitigation measure, thanks to detecting potential equipment failures before they cause a safety hazard. With advanced analytics, AI algorithms can identify abnormalities that signal impending failures, enabling maintenance teams to intervene quickly. This approach protects staff and assets and prevents costly downtime and environmental hazards.
Improved Reliability
IoT technology is key in increasing equipment reliability by continuously monitoring asset health and performance metrics. IoT sensors provide valuable insight into equipment health, helping maintenance teams identify and prioritize tasks effectively.
For example, in aviation manufacturing, PdM systems integrated with IoT sensors continuously monitor aircraft engines in real-time. Detecting anomalies and potential failures ahead of time, these systems facilitate proactive maintenance, guaranteeing the reliability and safety of fleets. This proactive approach significantly reduces the risk of in-flight failures, fostering trust and confidence among passengers and airlines alike.
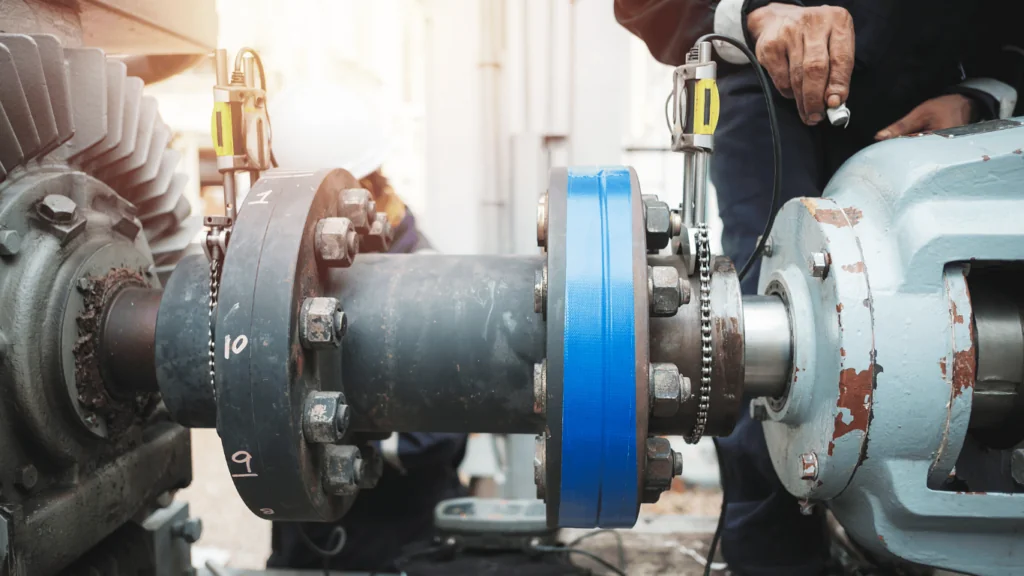
Compliance with Safety Regulations
Another example is how predictive maintenance systems with IoT sensors monitor critical infrastructure. In the oil and gas industry, for example, by detecting corrosion, leaks, and other potential hazards early, these systems help comply with stringent safety standards and environmental regulations. As a result, the risk of accidents is reduced, and compliance with industry regulations is ensured.
Discover AI-Powered Predictive Maintenance in Manufacturing
To learn more about AI-based predictive maintenance and its applications in manufacturing, please visit our dedicated page on AI in manufacturing. Here, you will find sample services and use cases illustrating the transformative potential of AI technology in optimizing production processes.
Moreover, NeuroSYS offers a 1h free AI consultation session to explore how AI can adapt to your business’s challenges and opportunities. Take this opportunity to discover AI use cases that can drive your organization’s innovation, efficiency, and growth.
