Downtime across industries can be staggering, costing up to $260,000 per hour in manufacturing (Aberdeen Group), $700,000 per day in oil and gas (McKinsey), $22,000 per minute in automotive (IHS Markit). However, AI technologies offer a proactive solution. Producers can reduce downtime with AI technology through predictive maintenance, real-time monitoring, and process optimization, enhance supply chain efficiency, and maximize productivity. Below, you can explore 10 ways to increase productivity and reduce downtime with AI.
Predictive Maintenance with Computer Vision
Let’s start with systems using advanced computer vision techniques. These are vision devices, mainly cameras, that collect data on machine operation and transmit it to software equipped with computer vision algorithms. This technology extracts information such as stain patterns, anomalies, and component degradation. By constantly monitoring equipment in real-time, they detect subtle changes and irregularities that indicate impending failures, which helps reduce downtime with AI.
For example, vision systems and computer vision technology can detect signs of wear, corrosion or cracks in machine parts by analyzing images captured by a camera. Moreover, it is perfect for detecting the presence of PPE in industrial plants. Predictive maintenance algorithms can predict potential equipment failures by comparing these visual cues with historical data and predefined thresholds.
Similarly, on-board cameras monitor components such as engines, brakes, and suspension systems in the transportation sector. Computer vision algorithms detect abnormalities such as leaks, overheating, or structural damage, enabling fleet managers to take preventive actions to avoid breakdowns and ensure safety.
Download this free e-book and discover all the applications of AI computer vision in manufacturing.
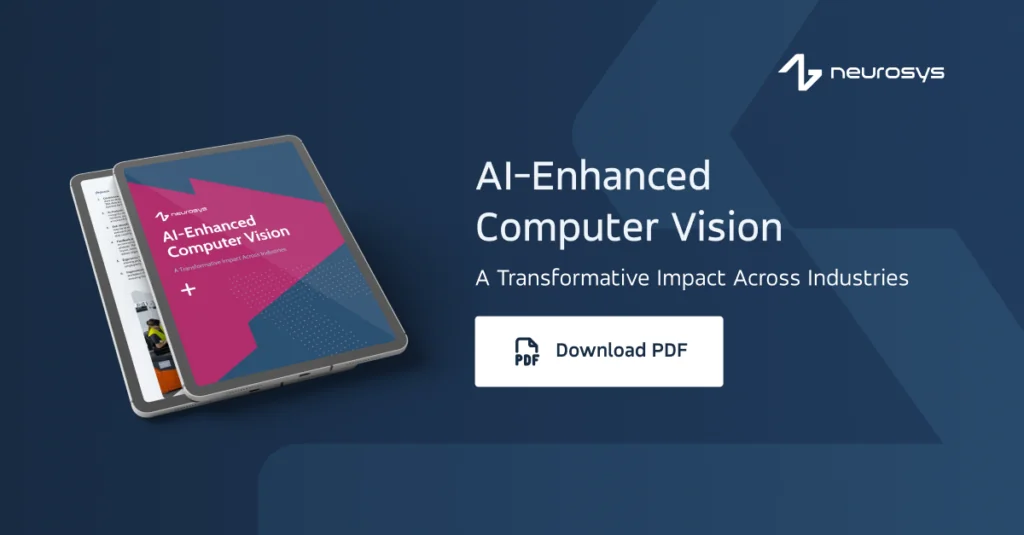
Optimized Scheduling with IoT Integration
Another way to reduce downtime with AI is to use AI to transform industrial schedules. This connects AI to Internet-of-Things (IoT) sensors throughout an industrial facility, allowing these algorithms to access data from sensors in machines, equipment, and the environment. Based on this, they can change production schedules, correlating them with machine performance, inventory levels, environmental conditions, and crew availability.
Additionally, they can prioritize other machines or modify production volumes to minimize interruptions and maximize efficiency.
Camera As a Sensor in Quality Control
Using cameras as quality control sensors reduces downtime in numerous ways:
- First, they monitor in real-time to discover abnormalities and deviations from standards.
- Second, visual inspections using computer vision technology speed up quality control by spotting faults or irregularities without operator intervention.
- Third, cameras monitor equipment health and predict maintenance needs before failure.
- Fourth, they help quality assurance by recording manufacturing quality details for faster troubleshooting and preventive steps.
Cameras functioning as sensors play a crucial role in optimizing operations by identifying inefficiencies and bottlenecks, thus reducing downtime and increasing productivity. Remote monitoring and diagnostics enable swift troubleshooting without on-site assistance, reducing travel and reaction times. Leveraging cameras as sensors not only enhances visualization and product quality but also improves operating efficiency, all of which ultimately contribute to the goal to reduce downtime with AI.
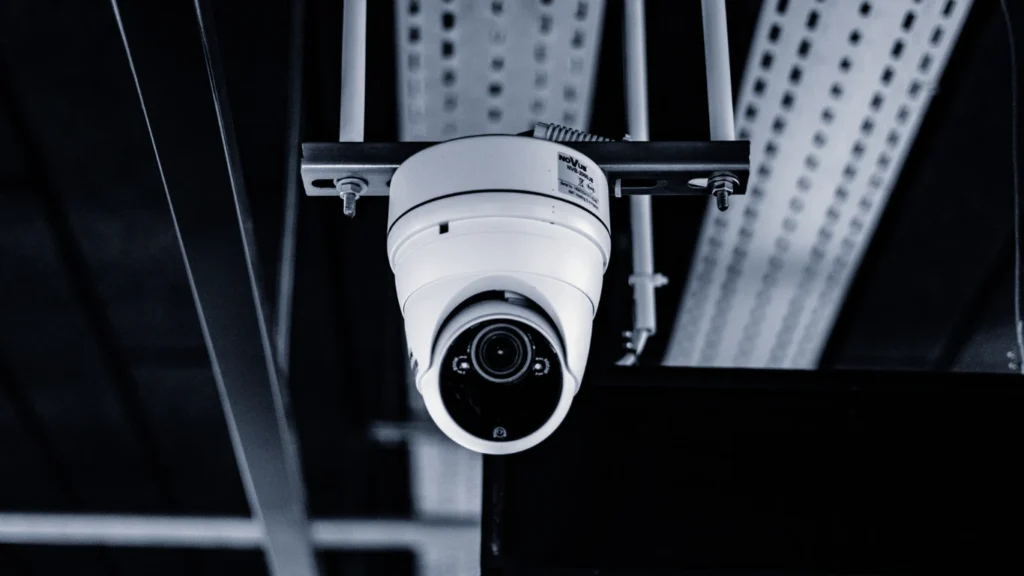
Reduce Downtime with AI Through Robotic Process Automation (RPA)
AI-powered data solutions can significantly optimize supply chain operations and reduce downtime by analyzing massive amounts of data from various sources and applying advanced analytical techniques.
First, they amalgamate data from diverse sources: suppliers, manufacturers, distributors, retailers, and external variables like weather, geopolitical shifts, and market trends. AI algorithms that automatically correct errors, manage missing values, and standardize formats across sources facilitate rigorous data cleansing and preparation before analysis to ensure precision and coherence.
On the other hand, by leveraging historical data, predictive analytics models anticipate future demand, supply chain disruptions, and market trajectories through machine learning (ML) algorithms that dig into patterns and correlations. Advanced demand forecasting techniques enable AI-powered solutions to accurately predict customer demand, analyzing historical sales data, market trends, and promotional activities to generate
Supply Chain Optimization with Data Processing Solutions
Showcasing how data processing tools enhance supply chains is crucial when you want to reduce downtime with AI. Because AI can simultaneously analyze diverse and voluminous data, its use helps improve demand forecasting, inventory management, supplier relationships, logistics operations, risk management and decision-making processes.
For example, AI can help CEOs assess supplier performance and optimize supplier relationships. By analyzing supplier data, including lead times, quality and price metrics, AI in manufacturing can identify opportunities for cost savings, risk reduction and supplier consolidation.
Additionally, AI-powered real-time monitoring solutions provide visibility into supply chain operations and key performance indicators. By analyzing data streams from IoT sensors and other sources, AI algorithms can detect anomalies, identify potential problems, and suggest actions to prevent disruptions and optimize supply chain performance.
Remote Monitoring and Management with IoT
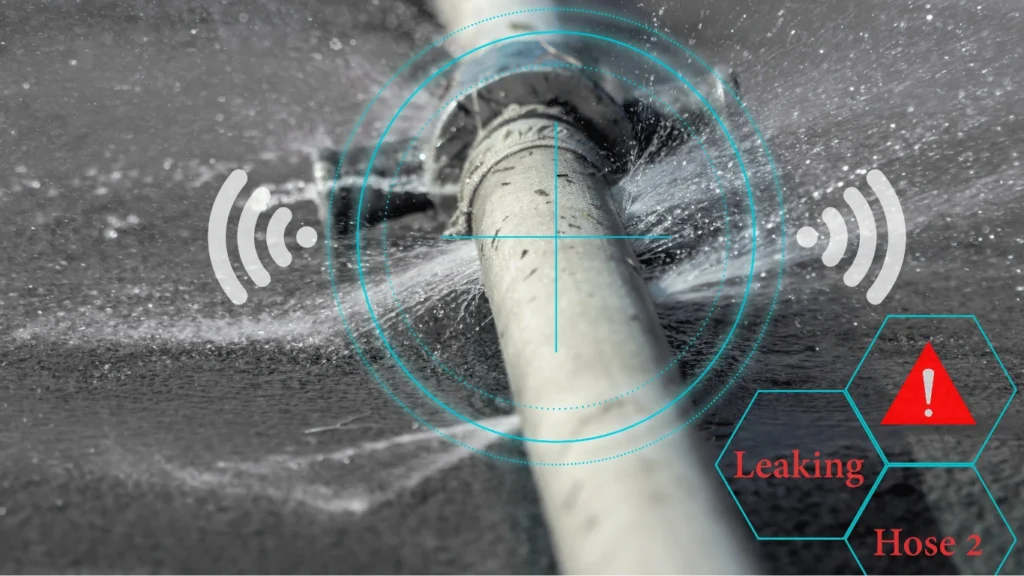
Internet-of-things devices with sensors (IoT) and AI-based software enable remote monitoring and management (RMM). RMM’s holistic approach to IoT minimizes downtime, increases operational efficiency, and delivers significant savings.
The IoT system continuously monitors machines, equipment, vehicles, and infrastructure from a distance. IoT devices (cameras, sensors) first collect and transmit data to the computer. The data is then analyzed in detail, and actions are taken on their basis, e.g., for maintenance or operation.
It is also worth noting that IoT devices can be integrated with existing service management systems, such as ticketing systems or enterprise resource planning (ERP) software. There, IoT technology improves communication and workflow digitalization, speeding up problem resolution.
Reduce Downtime with AI Through Smart Inventory Management
Reducing downtime and increasing productivity through intelligent inventory management can also benefit from using artificial intelligence technology and are another use case of artificial intelligence’s potential in manufacturing industry. Here is how:
- First, plant managers can integrate forecasting algorithms to analyze historical sales data and market trends. This helps predict future demand and optimize inventory levels to prevent stockouts or overstocking.
- Secondly, using predictive analytics software by analyzing supplier performance, order fulfillment time, and production capacity helps identify supply or production chain disruptions.
It is also worth investing in automated replenishment systems based on demand forecasts. These systems reduce errors and improve performance, enabling dynamic inventory adjustments according to demand and supply chain changes. These actions not only reduce downtime with AI but also increase productivity in inventory management.
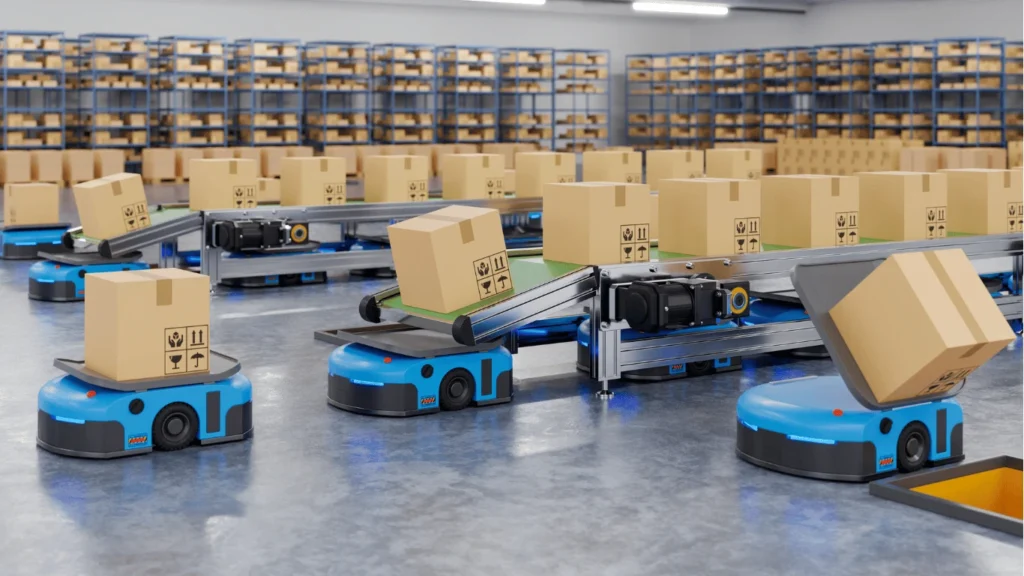
Augmented Reality-Driven Remote Inspections
Remote inspections using augmented reality (AR) can also significantly reduce industry downtime, as diagnosing equipment problems does not require physical presence at the plant. Remote inspections in industry using AI technology can be used for:
Remote equipment diagnostics
Using AR devices (smart glasses or tablets), technicians can inspect machines and equipment with remote expert support. They then have digital diagrams, checklists and maintenance instructions superimposed on the physical equipment. During this time, remote experts guide technicians through troubleshooting procedures from hundreds of miles away without the need to travel to the inspection site.
Emergency Repairs
Remote AR inspections enable rapid response and troubleshooting in equipment failure or emergencies. Remote experts can assess the situation in real-time, provide immediate guidance to on-site technicians, and remotely access diagnostic tools and documentation to speed repairs and minimize downtime.
Quality Control Inspections
Through remote quality control processes, AR technology enables inspectors to remotely review product specifications, inspect components or assemblies, and identify defects or nonconformances. This minimizes production delays and reduces business travel and working time costs.
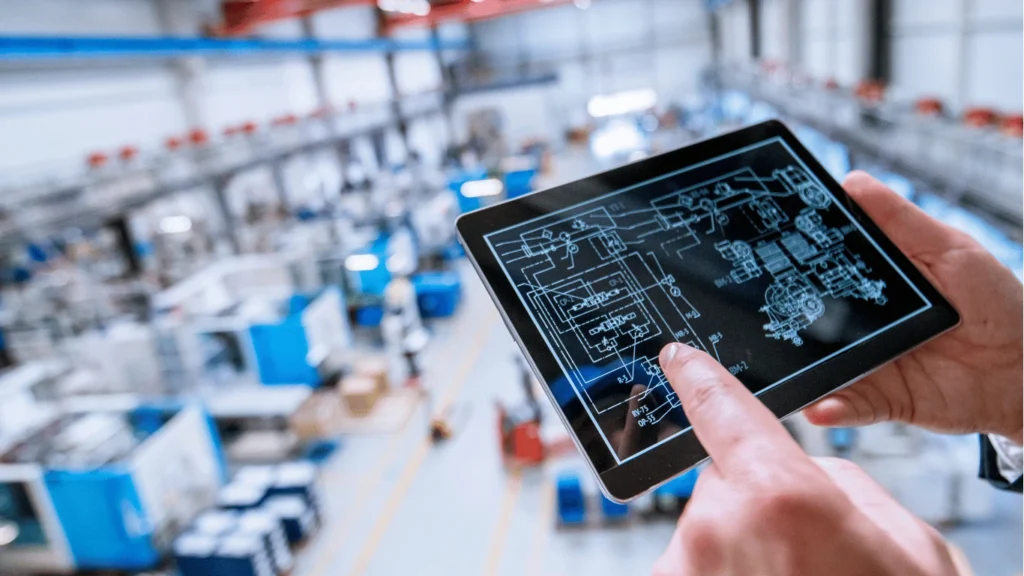
AI for Due Diligence
Predictive analytics can detect risks and opportunities, reducing downtime, costs and productivity while maintaining due diligence. Here is how AI technical due diligence can streamline productivity and reduce downtime:
- Risk Assessment – Predictive analytics algorithms can identify data trends that indicate supply chain disruptions, regulatory compliance issues, and financial instability.
- Financial Performance Forecast – Based on past financial data, market trends and other variables, predictive models can predict ROI, so companies can optimize capital allocation and avoid overpaying for weak assets, saving money and increasing profitability.
- Improved Operational Efficiency – Identifying process bottlenecks and optimization opportunities for the target company reduces downtime, increases productivity, and lowers costs.
- Predicting Consumer Behavior – Predictive analytics can analyze customer data to predict future behavior and preferences. This helps you improve your marketing, product and customer service plans, increase revenues and reduce customer acquisition costs.
Reduce Downtime With AI Workshop and 1-Hour Free Consultation
Through our AI Discovery Workshop, we thoroughly examine every aspect of your business, including operations, communication, production, and processes, identifying opportunities for AI-driven enhancements
What does it look like?
- AI experts work with stakeholders to identify critical pain points, such as equipment failures or supply chain disruptions, and assess data availability and quality, including equipment performance and inventory levels.
- On this basis, tailor-made AI solutions are proposed, such as predictive maintenance algorithms or demand forecasting models.
- The client receives an implementation plan detailing resources, ROI, schedule and potential challenges.
- In addition, the workshop company provides a cost-benefit analysis to help assess return on investment, and training and ongoing support guidelines ensure successful integration.
The “compact” version of AI workshops are ad hoc, single consultations with AI companies NeuroSYS offers. If you are just learning about the possibilities of AI technology in your industry and companies like yours, and you do not want to invest in more expensive consulting services, a 1-hour AI consultation is for you. During them, you will receive the necessary insights and recommendations to cut costs and reduce downtime with AI.
