Artificial intelligence algorithms are one of the tools increasingly used in industry, both in the work of engineers, traffic managers and machine operators. They support several activities, including planning, designing, implementing, managing and securing production in manufacturing plants.
Since the hype about AI has exploded, it has not been difficult to answer the question of how to improve productivity in manufacturing thanks to technologies. The problem is understanding which applications of AI technologies support processes. In this article, we focus on addressing how to improve productivity in manufacturing plants with the best AI strategies.
Downtime Reduction Strategies
To effectively reduce downtime in manufacturing operations, COOs should consider integrating AI-based strategies. Specific ones that improve maintenance, monitoring and process optimization. Here are some practical approaches and how to apply them:
Predictive Maintenance with IoT Sensors and Data Analytics
By implementing IoT sensors in your equipment, you can record real-time data on critical parameters such as temperature, vibration and pressure. Analyzing this data with advanced analytics allows you to predict when equipment may fail, enabling timely maintenance.
Examples:
- In predictive maintenance, thanks to machine learning algorithms, noticing increased vibration from a conveyor belt motor may signal the need for maintenance before failure occurs.
- Digital twins (virtual models of physical systems) help simulate different scenarios to predict outcomes. This prevents downtime and facilitates safer testing and optimization of equipment in harsh industrial environments.
Condition Monitoring Systems Using Computer Vision
Implementing computer vision technologies (object detection, camera as a sensor) enables continuous visual monitoring of machines. This technology uses object detection algorithms to identify anomalies such as misalignment, wear, or poor conveyor belt positioning. As we know, many of them may not be immediately visible to the human eye.
An example of computer vision benefits in manufacturing may be the production of glass vials, where computer vision systems detect cracks in products at an early stage. This early detection allows defective items to be removed before further processing, thus saving both time and resources. Another application is PPE detection (personal protective equipment detection) in production plans, where cameras conduct an initial visual inspection to detect whether workers wear PPE.
Download this free e-book and discover how to improve productivity in manufacturing with computer vision!
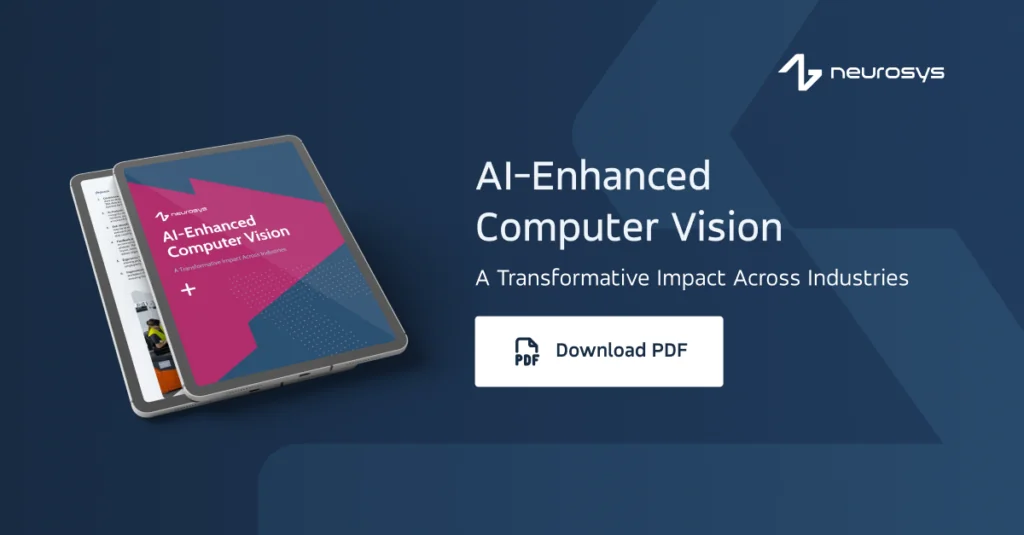
Continuous Improvement Culture with Machine Learning
Machine learning allows manufacturing companies to analyze large databases, which can be used to identify production hotspots and suggest possible optimizations. Applying these insights regularly improves operational efficiency and minimizes the risk of downtime.
For example, by analyzing data from filling machines, machine learning models may recommend slightly reducing container filling speed during peak hours. This will avoid frequent congestion and reduce downtime with AI.
Remote Inspections and Maintenance
Remote inspections and maintenance are revolutionizing cost reduction for manufacturing companies by integrating advanced technologies such as augmented reality (AR), computer vision, drones, and remotely controlled robots. Here are strategy of how to improve productivity in manufacturing through these methods:
Internet-of-Things
It is worth considering implementing IoT systems in large and wealthy production plants. Here, AI computer vision algorithms control sensors and cameras mounted on drones and remotely controlled robots.
Their job includes identifying potential problems such as design weaknesses, leaks or faulty parts. By detecting them, they speed up the inspection process and reduce the need for a human to be physically present during the inspection. This, firstly, reduces the costs of business travel, and secondly, it minimizes the need to send people to work in dangerous conditions.
How to Improve Productivity With Augmented Reality
Another answer to improving productivity in manufacturing is augmented reality (AR), which allows you to superimpose computer-generated elements on physical objects in the production plant. On the other side sits a remote inspector who can send checklists or repair diagrams (in video, photo, or document format) to technicians in real-time, displayed directly on AR glasses or tablets.
For example, if a machine part becomes damaged, a technician can use AR to display a detailed diagram of the damaged part, showing exactly where adjustments or replacements need to be made, even from a remote location. This significantly improves problem-solving and repair processes, reduces the costs associated with an inspector visiting the facility and accelerates the acquisition of experience by technicians.
Data Processing and Data Utilization
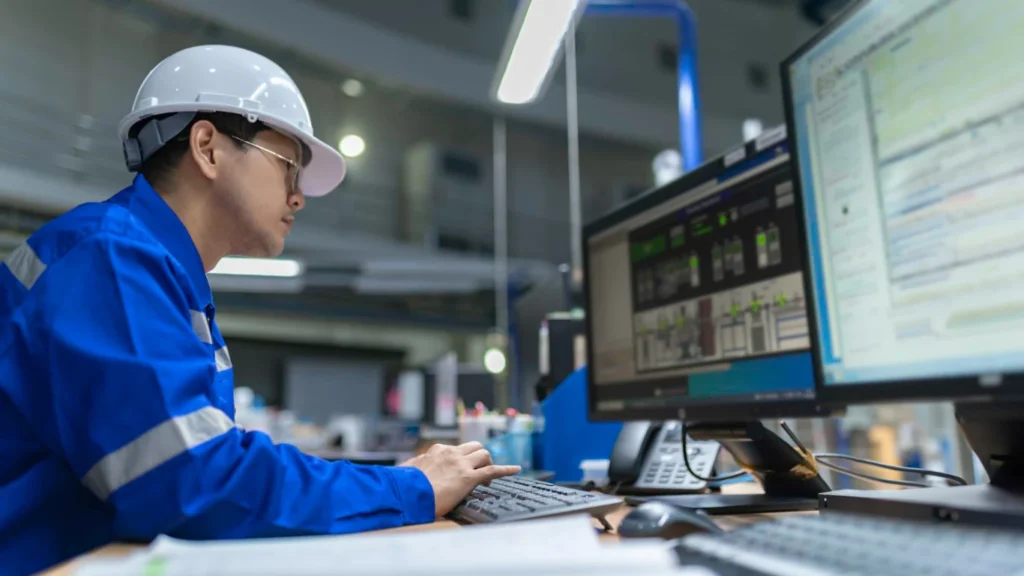
Are you wondering how to improve productivity in manufacturing using data science? Here’s how to put these innovations into practice:
Data Management Systems
Implementing data management can help manufacturing managers collect, store, and analyze the vast amounts of production data necessary to monitor various operational metrics and provide essential input for further AI analysis.
Importantly, this is not just about simple operating parameters or spotting patterns, as artificial intelligence offers digital twins. These virtual replicas of physical production processes enable real-time monitoring and optimization. This gives manufacturing companies data to test changes and predict results in a virtual space without disrupting real production.
Advanced Analytics and Deep Learning
Using advanced analytical algorithms and deep learning increases the ability to sift through huge data sets. In this way, artificial intelligence helps detect hidden patterns and anomalies and predicts future trends that may be missed by traditional analysis methods.
For example, deep learning algorithms identify frequent overheating events in a specific part of the assembly line under specific operating loads. This knowledge enables maintenance planning to replace or repair a faulty component before it fails. This is definitely a way to reduce downtime with AI worth considering.
How to Improve Productivity With AI-Driven Predictive Modeling
Another application of AI in data science are predictive modeling techniques. They effectively estimate demand and optimize production schedules to match market demand, reducing waste and improving inventory management.
For example, predictive modeling based on artificial intelligence is particularly useful in plants producing seasonal products. These technologies analyze sales history, market trends and production capacity and then recommend production volumes, eliminating overproduction and inventory shortages.
Predictive modeling techniques also improve resource allocation by forecasting machine uptime, scheduling maintenance to avoid interruptions, and matching labor levels to production needs.
Automation in Supply Chain and Inventory Management
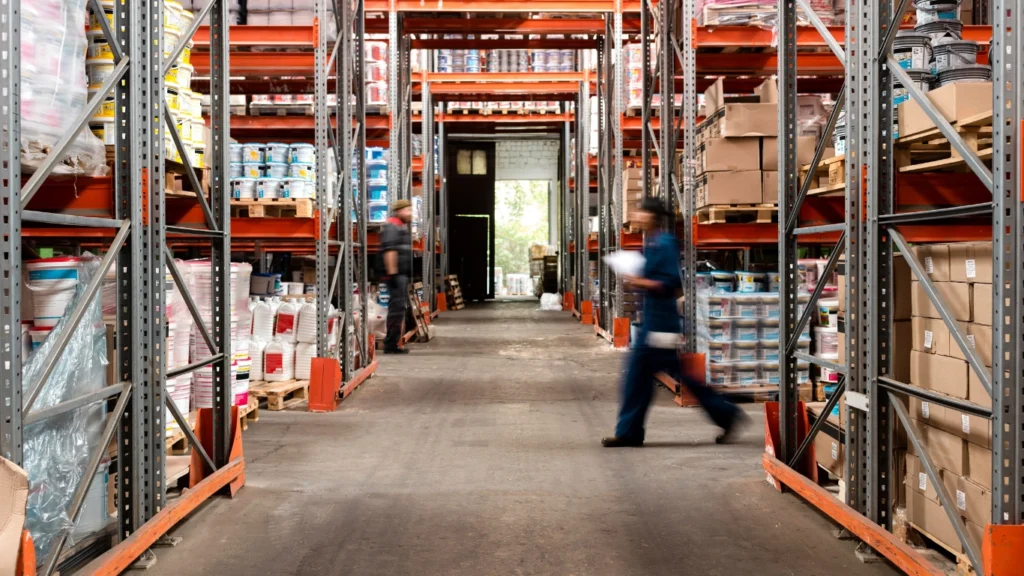
Automation in supply chain and inventory management boosts efficiency and accuracy, demonstrating how to improve productivity in manufacturing. It streamlines processes, reduces errors, and optimizes logistics, leading to faster production cycles and better resource management. Additionally, it provides real-time data for informed decision-making, enhancing responsiveness to market shifts. Now let’s explore some of the best AI-driven approaches:
Automated Material Handling
To increase productivity in manufacturing, companies should also invest in integrating robotics and automated conveyor systems. These technologies ensure that materials move efficiently around the production floor, significantly reducing the need for manual work and minimizing human errors.
The capabilities of these systems can be increased by using the above-mentioned digital twins, here: by creating virtual models of supply chains. Such models integrate data in real-time, providing comprehensive visibility into inventory levels, the condition of materials as they move through the supply chain, shipment statuses and potential bottlenecks.
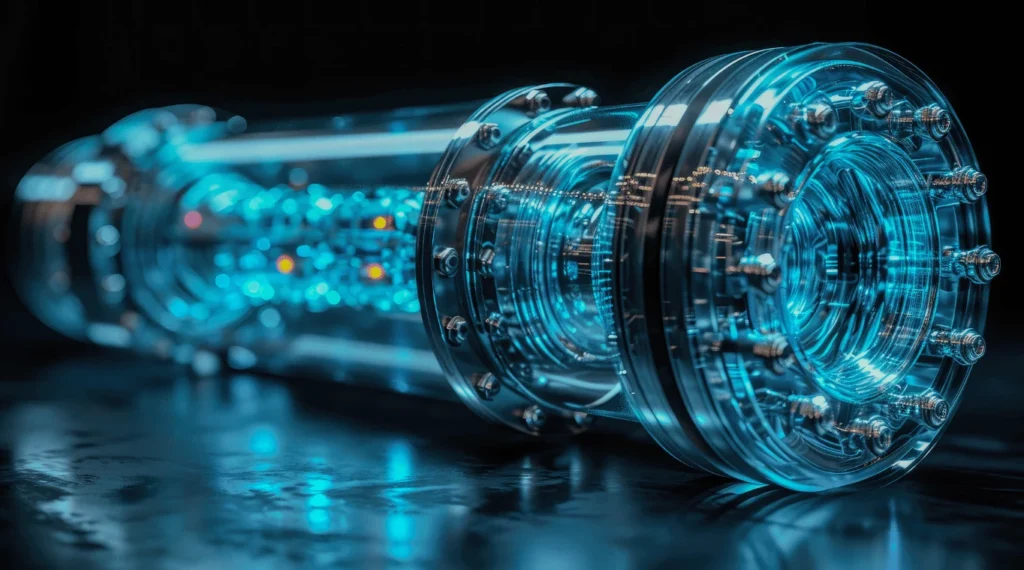
Precise Inventory Management and Tracking
Another way to demonstrate how to improve productivity in manufacturing is by utilizing computer vision-aided RFID technology and barcode scanners to manage and track inventory accurately. These technologies establish a precise system for monitoring inventory items at every stage of the supply chain. Computer vision technology enhances the functionality of RFID and barcode scanners, enabling rapid identification and verification of items at various checkpoints.
For example, computer vision-aided warehouse systems can automatically verify incoming and outgoing shipments against inventory lists. By reporting discrepancies in real-time, they maintain constant accuracy in inventory records. Such innovations not only enhance inventory management but also significantly increase manufacturing operations’ overall efficiency and productivity.
Future Outlook and Innovation
Without a doubt, work on global productivity improvement should be combined with investments in research and development. By adopting new AI-based technologies, manufacturers can create more transparent and efficient supply chains. This transparency leads to better decision flow and better coordination.
Moreover, it seems that AI in manufacturing will continue to transform Industry 4.0, for example by minimizing human intervention and reducing rejects and material waste. Adaptive production processes also have great potential as they adapt, for example, to the quality of materials or machine behavior and can meet individualized production requirements more quickly.
How To Improve Productivity And Preserve Employee Safety
Finally, a few words about how to improve productivity in manufacturing by taking care of the health and safety of people on site. Regardless of the pace of technology development, with AI at the forefront, most analysts agree that technology will never be able to eliminate human work, and it is not only about simple jobs. Therefore, it is important that the prospects for technology development also consider the aspect of human work safety and employee well-being in industrial plants.
As highlighted in the study “Enhancing Employee Productivity Through Technology System AI-Based Approaches,” AI systems allow HR teams to prioritize employee well-being initiatives by automating routine tasks and providing instant support through LLM algorithms (chatbots and virtual assistants). Here are some ideas on how artificial intelligence can come in handy:
Computer vision for monitoring and compliance
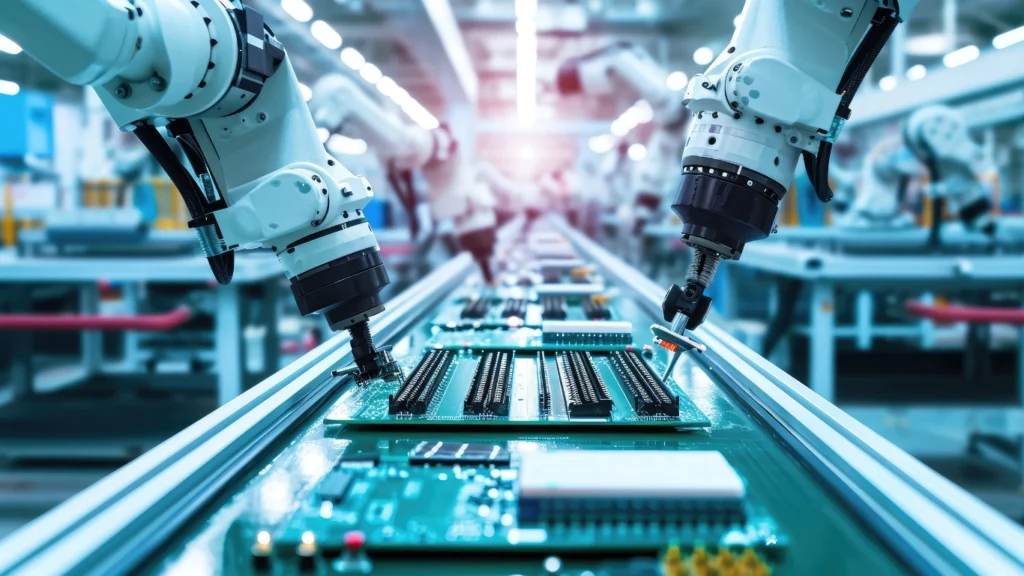
Computer vision systems provide visual inspection and can be used to detect unsafe behavior and identify situations where a machine is being operated unsafely. These systems reduce the risk of accidents and injuries by ensuring safety protocols are followed, leading to less downtime and higher productivity.
Predictive analytics to prevent accidents
AI-powered predictive analytics evaluates patterns and trends based on past incidents and operational data, enabling proactive risk management. Facilities can address these hazards before they lead to accidents, effectively minimizing disruption and increasing employee safety.
Digital twins and AR for simulation and training
Digital twins and augmented reality can simulate scenarios to predict outcomes under various conditions without risking real-world operations. They are also used to train employees in a virtual environment. With this training, employees are better prepared to deal with unexpected situations, reducing accidents and improving overall performance.
How to improve productivity with Portable health monitoring devices
AI-powered mobile devices have several features. They can monitor employee health and fatigue levels in real-time and then alert employees and supervisors if they show signs of fatigue or other health problems that could lead to accidents or reduce productivity. This allows plants to maintain a healthier and more alert workforce.
How To Improve Productivity In Your Company – Book An AI consultation
Applying technologies such as digital twins, computer vision, deep learning, and artificial intelligence fosters a culture of continuous innovation and improvement, directly addressing how to improve productivity in manufacturing plants. These tools offer solutions to numerous industrial challenges, enhancing monitoring accuracy, optimizing resource allocation, and minimizing operational downtime. Manufacturers leveraging these AI-driven approaches can expect significant efficiency and production capabilities enhancements.
To learn how AI-powered strategies can bring tangible benefits to your manufacturing processes, book a 1-hour free consultation with an AI expert from NeuroSYS. This session can provide you with tailored insight into integrating these revolutionary technologies into your business.
